製造業界は長年、熟練した職人の技術と独自のノウハウによって支えられてきました。
しかし、AIやデジタルテクノロジーの急速な進化は、業界に大きな変革をもたらしています。
日本の製造業のこれからには、DXの採用が不可欠です。
DXとは、企業がデジタル技術を利用してビジネスモデルや業務プロセスを根本的に変革する考え方です。
本記事では、製造業におけるDXについて、弊社の具体的な実績を事例に挙げながら、課題や推進方法について詳しく解説します。
製造業のDXとは:デジタル化のその先
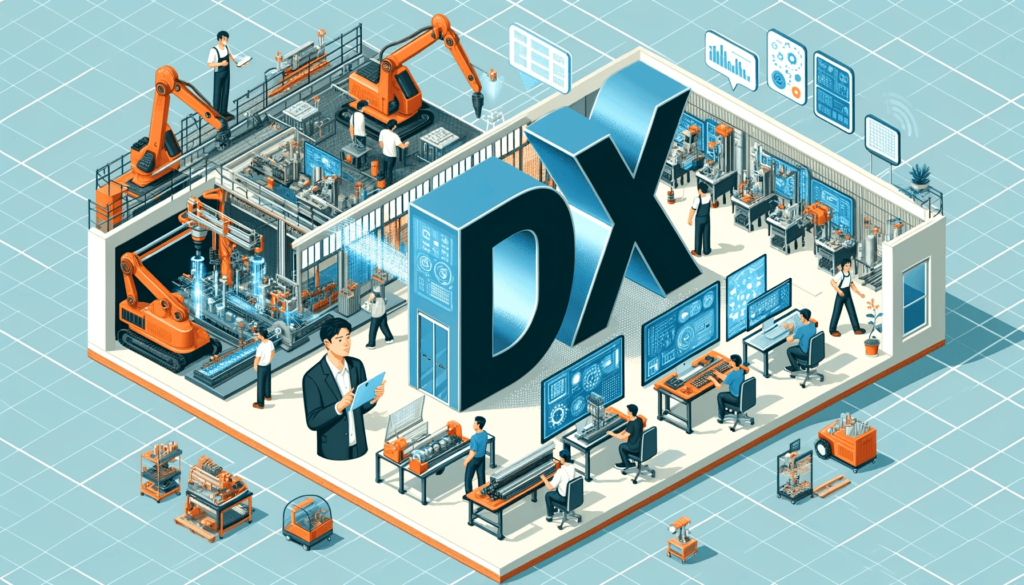
デジタルトランスフォーメーション(DX)は、企業がデジタル技術を活用してビジネスモデル、業務プロセス、そして企業文化を根本的に変革する過程を指します。
この変革は、業務の単なるデジタル化を超え、新たな価値創造、顧客体験の向上、競争力の高め方を目指します。
AIのような先進技術を駆使して、データ駆動型の意思決定を可能にし、効率化とイノベーションを実現します。製造業におけるDXは、単に作業の効率化を図るだけでなく、最終的には製品を使用する人々の生活の質を高めていくのです。
製造業におけるDXの重要性:伝統と革新の融合
製造業でのDXは生産性と品質の向上、市場での競争力の強化に不可欠です。
デジタルツールを導入することで、製造プロセスを効率化し、エラーを削減し、リアルタイムのデータ分析に基づく意思決定が可能になります。
データの一元管理により、企業内でのノウハウや技術の蓄積が容易になり、情報共有を効率的なものにします。
これにより、企業は日々変化する市場環境に迅速かつ柔軟に対応する能力を高めていくのです。
さらに、DXは既存の作業にかかる時間を削減し、新しい技術開発やイノベーションにリソースを集中できるようにします。
これにより、製造業はデータの可視化、ダイナミックな能力の強化、人材の代替手段としての活用、生産効率の向上など、経済の波に乗り遅れることなく、世界基準の発展を達成することができるのです。
DXの事例にみる取り組む前の課題
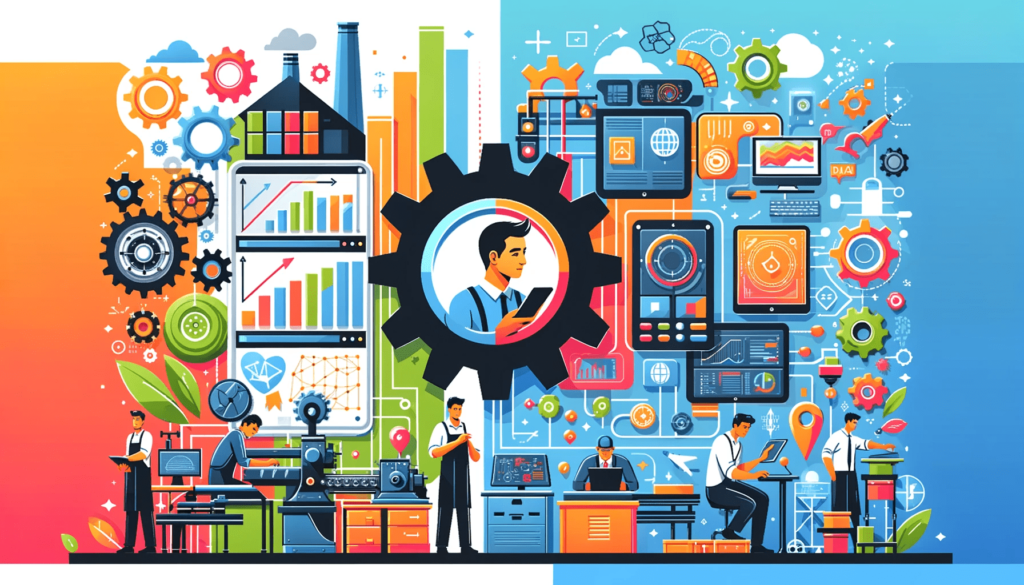
今回、DXに取り組んだ企業様には2つの面での課題がありました。
- 経営者視点の課題
- 現場の課題
それぞれ掘り下げます。
1. 経営視点の課題
経営視点からみた課題は「工場の生産性の向上」です。
工場全体の生産性を向上させるためには、製品ごとに変わる制作工程に合わせて、複数ある機械を効率的に動かさなければいけません。
弊社にご相談いただく前は、工場にある機械ごとに「1週間の稼働票」などのエクセルが用意されている状況でした。
経営層が知りたい情報ごとに個別にエクセルを用意する形で対応しているため複数のファイルを管理しなければならないのです。
また、入力の元となるデータは現場のスタッフが手入力で記載した用紙ですから、正確性も十分とは言えません。
これらの状況をデータで可視化するため、タブレット端末でのデータ入力とそのデータを管理するツールが必要であると経営層は考えていました。
2. 現場の課題
現場のスタッフにヒアリングすると「ミスを減らしたい」という経営層とは違った課題があることに気づきました。
アナログな管理だからこその伝達ミスが多発していたのです。
たとえば、工場で生産した製品は検針を経て出荷されますが、検針をしたいタイミングになっても製品が仕上がっていない、そのため急ピッチで検針を進める必要があるような日もあったのです。
また、プラスチックの工場ですから機械の温度が低くなると製品の品質も低下するため、温度管理も非常に重要な工程です。
しかし実際の現場では職人の感覚で作業が進められており、忙しさやちょっとしたミスから出荷できない不良品が発生することもしばしば。
さらに、製造以前の材料の管理がかなり複雑になっているのも問題点として挙げられました。
プラスチックの製品をつくるにあたり原材料や塗料を組み合わせるのですが、その管理番号に法則性がなく、どの番号がどの材料を指しているのかは職人さんの記憶頼りといった状況。
こうした職人さんの技術や経験に依存する体制から来るミスを減らしたい。そのために各工程を可視化したいというのが現場の課題でした。
製造工場のDX化は一筋縄ではいかない
製造業には製造業ならではのDXの難しさがあります。
今回もやはり、次の3つがDX化を進める上での課題となりました。
- 生産性の向上にはデータと時間が必要
- 現場スタッフも把握できていない管理番号
- 新しいシステムを職人さんが使えるか
それぞれ、弊社の対応を含めご紹介します。
生産性の向上にはデータと時間が必要
経営者には、DXによって工場の生産状況を可視化して効率化し、売り上げを上げたいという希望があります。
確かにアナログ管理である現状を改善すれば生産性は向上するでしょう。
しかし、システムを導入すればよいというものではなく、効率化には現状を把握するデータをそこから試行錯誤する工夫の時間が必要なのです。
具体例を挙げてみます。今回のプラスチック工場では塗料を使います。塗料や材料を変える際には機械を洗浄する必要があるのです。
DX化によって生産性を向上させるというのは、こうした機械洗浄のタイミングや機械のクールダウンのタイムロスを減らしていく作業です。
つまり現状の工程でデータを取得しながら効率化を図り、実際に効率的だった方法を採用していくという試行錯誤を必要とします。
経営層の脳内では、現場でタブレット入力したデータをチェックして細かい部分を詰めていき売り上げが上がるイメージがありましたが、実際には時間をかけて実現するもの。
DXによる生産性の向上は長期的に実現するものと捉える方がよいでしょう。
現場スタッフも把握できていない管理番号
経営年数が長い工場であるほど、材料や製品の管理番号が複雑化するケースが増えます。
今回も例外ではなく、管理番号は非常に複雑なものでした。
これまでの作業方法で進めるのであれば職人さんがわかってさえいれば問題なかったのですが、システムで管理するとなるとそうはいきません。
職人さんがうろ覚えの材料まですべてもれなくチェックしていきます。
弊社はスタッフが実際に現地に足を運び、職人さんから聞き取りをして管理体制を整えていきます。
ときには片道数時間の現場に10回訪問するケースもあり、今回も何度か訪問させていただきました。
新しいシステムを職人さんが使えるか
DXは単なるIT化ではなく、従業員や顧客を含め、関係者の利便性を向上させなければ意味がありません。
そんななか、製造業の工場ではご年配の職人さんも多く、これまで数十年決まった流れで業務を遂行してきた場合もあります。
DX化を理由にシステムを印新したとして、職人さんが使えなければ業務効率は逆に下がってしまうでしょう。
これまでのやり方をなるべく変えずに、それでいてミスを減らし、生産性を上げられるようなシステムでなければいけません。
こうした状況を踏まえ、弊社では部分的なシステム導入から改善を繰り返しつつ、徐々に工場全体へと浸透させていくよう努めております。
まとめ
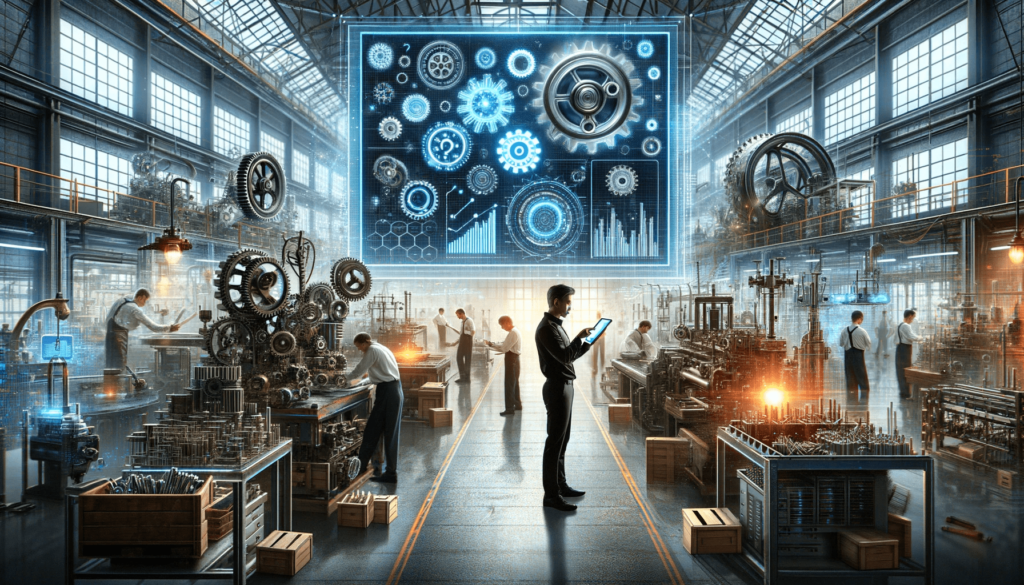
製造業にとってDXはもはや、避けては通れないものになりつつあります。
一方で、従来のやり方から大きく変えてしまうようでは現場の混乱を招いてしまうでしょう。
経営者が望むような売り上げに貢献するような変化をもたらしながら、現場の職人さんの仕事を守るためには工夫が要ることも事実です。
今回はそういった事情の一例として、弊社実績を交えて課題や向き合い方を解説しました。
弊社では、製造業の企業からのDXのご相談を承っております。
助成金の活用などご提案もございますので、お気軽にお問い合わせください。